In a fabrication workshop, efficiency matters. When manufacturing tanks, pressure vessels, and piping systems, every step in the process impacts time, cost, and final quality. One challenge that often comes up is flange surface damage after welding. Heat distortion, spatter, and handling marks can leave flanges uneven, which can lead to sealing issues down the line.
When this happens, there are usually two options:
- Cut off the flange and weld on a new one
- Reface the existing flange
Cutting and replacing might seem like the obvious choice, but it adds extra work and cost. In many cases, refacing the flange is a faster and more practical approach. The Normaco Manual Facer provides an easy way to restore flange surfaces in-house, without needing power tools or outsourcing the work.
Why Not Just Cut and Replace?
Removing a damaged flange and welding on a new one adds several steps to the process:
- Cutting off the old flange
- Preparing and aligning the new flange
- Welding and any necessary post-weld treatments
- Dimensional checks and possible rework if alignment is off
All of this takes time and increases material costs. Welding also introduces additional heat input, which can cause further distortion—especially in pressure vessels and large tank assemblies, where precision is critical.
In contrast, refacing the existing flange avoids most of these issues. With a manual flange facer, the surface can be restored in place, often in a fraction of the time.
The Benefits of Manual Flange Refacing in Fabrication
For workshops working on pressure vessels, tanks, and piping systems, a manual flange facer offers:
✔️ Lower Material Costs – No need to buy a replacement flange.
✔️ Faster Repairs – Refacing takes minutes or hours, not days.
✔️ Less Welding Work – Reduces risk of distortion and alignment issues.
✔️ No Need for Power – Can be used anywhere, even on large vessels.
✔️ Precision Results – Ensures smooth, even flange faces for better sealing.
Many fabricators already use manual flange facers for on-site repairs, but they are just as useful in the workshop. Instead of spending time cutting, aligning, and welding new flanges, a simple refacing job can get the part back on track with minimal downtime.
A Practical Approach to Flange Repairs
If a flange is severely damaged beyond repair, replacement is necessary. But in many cases, refacing does the job faster and at a lower cost.
For workshops handling pressure vessel fabrication, tank manufacturing, and industrial piping, having a reliable flange facer on hand makes sense. It’s a small investment that can reduce work, save materials, and improve efficiency—all while maintaining the quality standards required in fabrication. Read more about our manual facer here.
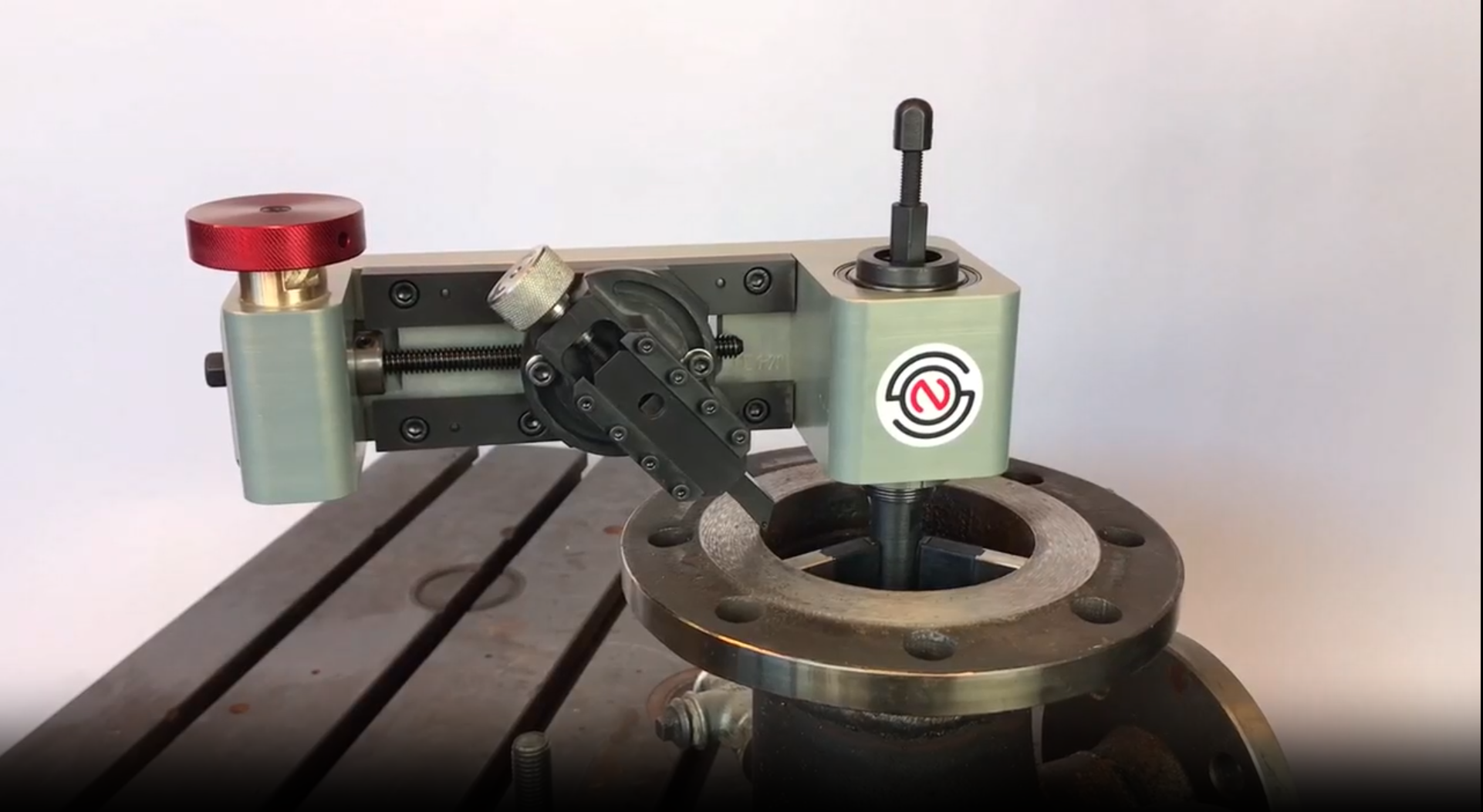