Bolt Saw vs. Nut splitter
During maintenance work, flanged connections often require opening. Nuts on the flanges can become heavily corroded due to prolonged exposure to the elements. To address this, nut splitters are commonly employed, utilizing hydraulic cylinders to split the nut in half. However, nut splitters come with their own set of challenges. The splitting head covers only a specific range of nut sizes, necessitating the use of multiple splitting heads to cover a wide range, which can be costly. Larger nut splitting heads are also cumbersome and may require multiple persons or lifting devices for manipulation. Additionally, there are safety concerns associated with hydraulic pressure buildup during operation and the uncontrollable release of pressure when the nut breaks.
An alternative method for this task is the Flange Bolt Cutting Saw, which offers several advantages. With a single machine, it can cut a large range of studs up to M72. Its clamping range is extensive, offering versatility in use. Furthermore, the Bolt Saw is lightweight and can be set up by a single operator due to its modular construction. The cutting operation is spark-free and safe, thanks to the low cutting speed and pneumatic motor. These features make the Bolt Saw an excellent choice for hazardous environments where spark-free work methods are preferred.
Pros
- Lightweight, easy to carry to the site.
- Lower investment cost compared to nut splitters
- Spark free work
- Easy to operate and maintain
Cons
- Requires a gap between flanges
- Requires space around flanges.
- Blades require sharpening.
Read more about Normaco's Flange Bolt Saw here.
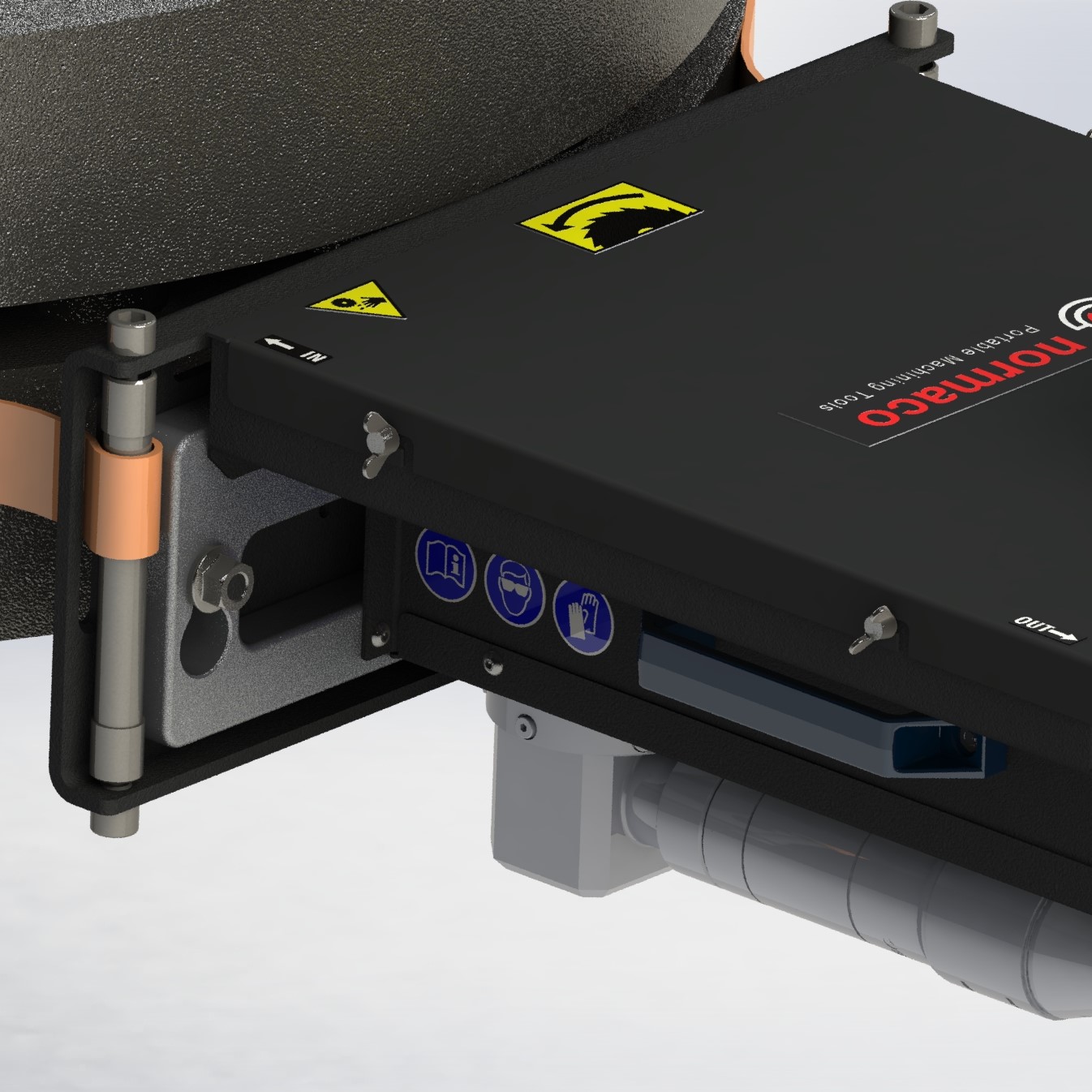